Verso un’ulteriore semplificazione del cantiere
Dei vari tipi di Afs, automatic feeding systems, presenti sul mercato, qui ci si concentra sui sistemi di distribuzione della razione in cui il livello di automatizzazione è tale da comprendere tutti gli step operativi: dal carico e trasporto degli ingredienti fino alla distribuzione finale del piatto. Uno studio del Crea di Treviglio nell’ambito del progetto Autofeed
INFORMATORE ZOOTECNICO n. 20-2021 22 novembre
La tecnologia di somministrazione robotizzata della razione bovina (Automatic Feeding System, Afs) continua la sua evoluzione verso sistemi sempre più automatizzati. Ne consegue un progressivo affrancamento degli operatori dalla preparazione diretta della razione (lavoro esecutivo, ripetitivo e molto rigido in termini di orari), in favore di ruoli sempre più gestionali e manageriali (Bisaglia et al., 2008).
A questa prima, evidente, ricaduta ne fanno seguito altre, probabilmente meno esplicite, legate a quest’innovazione: il benessere animale e la variabilità della razione dovuta all’errore umano per citare le principali [Andrighetto et al., 2016].
Costituisce, inoltre, una soluzione a minor impatto ambientale rispetto ai tradizionali metodi di somministrazione dell’unifeed, con una riduzione dei consumi energetici [Obershalz et al., 2015] conformemente con quanto auspicato dalla Politica agricola europea circa la sostenibilità dell’agricoltura [Ascione et al., 2021].
All’interno del progetto “Autofeed”, finanziato dalla Regione Lombardia nell’ambito della sottomisura 16.1 del Feasr – Programma di sviluppo rurale 2014-2020 (www.autofeed.crea.gov.it), si è voluto focalizzare l’attenzione sulle caratteristiche e sulle potenzialità dei sistemi completamente automatici per la distribuzione dell’unifeed.
Tre tipi di Afs
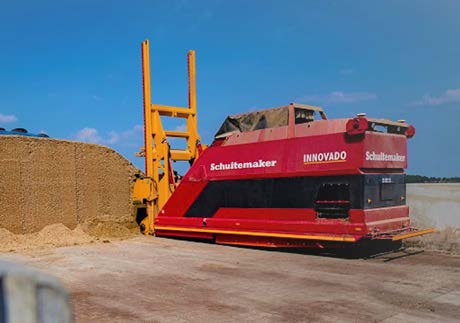
Esempi di carri miscelatori semoventi completamente automatizzati senza posto guida (fonte: https://www.agrartechnik.ch/; https://www.kuhn.fr/)
Ad oggi, sono disponibili tre tipi di Afs sul mercato:
– Tipo 1, in cui sono automatizzate le sole operazioni di trincia-miscelazione e distribuzione della razione;
– Tipo 2, le cui peculiarità prevedono che l’automatizzazione, oltre alla trincia-miscelazione e distribuzione della razione, consenta anche il riempimento del carro;
– Tipo 3, sistemi di distribuzione della razione in cui il livello di automatizzazione è tale da comprendere tutti gli step operativi: dal carico e trasporto degli ingredienti fino alla distribuzione finale del piatto unico [Haidn, 2015].
Con quest’articolo si pone l’attenzione sugli Afs appartenenti alla terza tipologia la cui tecnologia è ancora poco diffusa, ma che denota l’interesse ad un’ulteriore semplificazione del cantiere riducendo il ruolo degli stoccaggi temporanei (cucina) potendosi approvvigionare dai sili presenti in azienda direttamente o con minime modifiche.
Le tecnologie possibili
Il terzo livello di automazione prevede che tutte le fasi necessarie all’alimentazione degli animali siano rese automatiche. Ciò significa che il vagone miscelatore/distributore riceve, o addirittura preleva, i componenti della razione direttamente dai sili aziendali evitando lo
stoccaggio temporaneo dell’alimento durante il quale, la naturale degradazione cui gli ingredienti possono andare incontro, può causare ricadute sulla qualità della razione [Haidn, 2015].
Il principio di funzionamento di queste macchine è molto variabile e dipende principalmente dalla tecnologia che la casa produttrice ha voluto utilizzare. Incontriamo modelli che sfruttano le caratteristiche di movimentazione dei carri della tipologia 2, ovvero attraverso l’uso di guide magnetiche nel terreno, cui si aggiungono poi una desilatrice automatica direttamente in trincea, oppure troviamo dei vagoni appositamente sviluppati, di medie dimensioni, che sfruttano la tecnologia satellitare e laser per potersi muovere all’interno dell’allevamento in modo sicuro.
Di fondamentale importanza rimane la pavimentazione degli spazi deputati al passaggio del robot: questa deve, infatti, avere caratteristiche di pendenza, rugosità e attrito tali da permettere ai vagoni semoventi di operare senza difficoltà e senza scostamento dalla traiettoria impostata.
Infine, si stanno sviluppando carri miscelatori, anche di grosse dimensioni, che permettono all’allevatore di scegliere se automatizzare completamente la preparazione della razione oppure prendere il controllo del mezzo e preparare personalmente l’unifeed. Segue perciò, una descrizione dei modelli attualmente presenti e/o in fase di sviluppo.
I modelli presenti
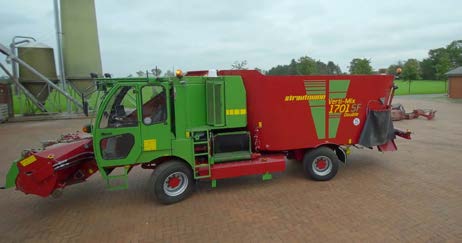
Esempi di carri semoventi automatizzati con posto guida (fonte: Strautmann Landmaschinen; https://www.hirl-mischwagen.de/)
Possiamo mettere a fuoco tre grandi tipologie di modelli: a) il vagone automatico semovente con desilatrice; b) il vagone miscelatore completamente automatico senza posto guida; c) il carro miscelatore automatico dotato di posto guida.
a) Vagone automatico semovente con desilatrice. Questo modello si basa sull’utilizzo di un vagone semovente di tipo 2 accoppiato ad una desilatrice automatica posta in corrispondenza di ogni silo orizzontale (figura A).
Il robot, grazie a specifiche guide magnetiche, raggiunge il silo e si posiziona al di sotto della desilatrice automatica in attesa che questa provveda allo scarico dell’alimento nella quantità prestabilita. Le desilatrici automatiche provvedono al taglio dell’insilato grazie ad un’apposita fresa per poi caricarlo all’interno del carro mediante un gruppo soffiante.
Tutto questo sistema è completamente elettrificato con ridotti costi energetici che si possono azzerare nel caso di autoproduzione dell’energia.
b) Vagone miscelatore completamente automatico senza posto guida. Il principio di funzionamento di questo sistema è simile a quello di un carro miscelatore convenzionale; tuttavia è
dotato di tecnologie che gli permettono di muoversi e distribuire autonomamente la razione (foto 1 e 2).
Il vagone automatico è dotato di una testata desilatrice con fresa adatta a tutte le tipologie di insilato; tramite un apposito nastro trasportatore l’alimento viene caricato all’interno del cassone (di dimensioni medio-piccole) dove, al completamento del carico di tutti gli ingredienti, verrà effettuata la trincia-miscelazione ad opera di apposite coclee dotate di coltelli.
Un’apposita interfaccia, su cui sono inserite le indicazioni dell’alimentarista aziendale, permette di gestire il carico degli alimenti sia come sequenza che come quantità. La stessa interfaccia computerizzata si occupa della gestione dello scarico in mangiatoia e del numero di distribuzioni giornaliere da effettuare. Lo scarico del prodotto miscelato avviene mediante apposito nastro trasportatore.
La parte più sviluppata, che permette il perfetto funzionamento della macchina, riguarda il sistema di navigazione; questi robot sono infatti dotati di due sistemi di guida automatica: il primo sfrutta la tecnologia Gps/Rtk mentre il secondo utilizza la tecnologia Lidar, ovvero una tecnologia basata su sistemi laser che rilevano la distanza e la presenza di eventuali ostacoli tra il punto in cui si trova il carro e quello di destinazione.
Allo stato attuale non è presente una motorizzazione elettrica per questi modelli di Afs, generalmente equipaggiati con motori diesel di media potenza. Queste macchine hanno il vantaggio di potersi adattare a qualsiasi tipo di allevamento, non necessitano di alcun locale apposito per lo stoccaggio temporaneo degli alimenti (a parte il consigliabile raggruppamento dei sili verticali per i mangimi) e possono, inoltre, affrontare dislivelli superiori rispetto alle attuali macchine a propulsione elettrica.
Resta, tuttavia, auspicabile che, con l’evoluzione dei sistemi di elettrificazione, anche questi Afs semoventi interamente automatizzati possano essere elettrificati anche in vista di una riduzione delle richieste di combustibili fossili.
c) Carro miscelatore automatico dotato di posto guida. In questo caso si tratta di un vero e proprio carro miscelatore semovente tradizionale, implementato con tecnologie che permettono sia la sola distribuzione automatica della razione sia la completa automazione di tutte le fasi di preparazione e distribuzione della stessa (foto 3 e 4). Attualmente non sono presenti modelli sul mercato, ma soltanto prototipi in fase sperimentale.
Il principio di funzionamento di queste macchine è paragonabile a quello di un carro convenzionale in cui la sola guida automatica viene resa possibile mediante:
– l’installazione di un sistema satellitare per la movimentazione all’interno degli spazi aperti dell’allevamento e per il carico degli insilati;
– l’installazione di scanner laser utili al rilevamento tridimensionale dell’ambiente circostante, per aumentare la precisione di taglio in trincea e per la movimentazione del carro stesso all’in
terno degli edifici stabulativi.
Per chi non è ancora pronto
Per gli allevatori che non sono ancora pronti ad effettuare un passaggio all’alimentazione completamente automatizzata il mercato propone anche vagoni trincia-miscelatori automatici e autocaricanti. Il sistema è molto simile alle tipologie di cui abbiamo già ampiamente parlato in un precedente articolo [Rossi et al., 2021]; tuttavia, è dotato, nella sua parte anteriore, di una fresa che permette il taglio e il successivo carico degli ingredienti (foto 5).
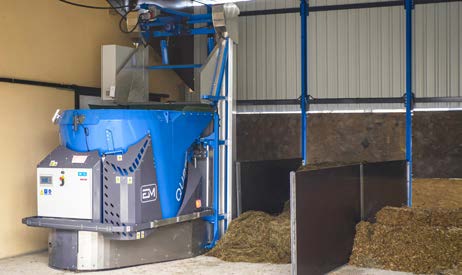
Vagone unifeed automatico e autocaricante e mini trincee contenenti gli ingredienti della razione (fonte: http://euromilk.pl/en/products/automation-feeding/tmrobot-OVGSRJ/ )
Questo sistema necessita comunque di un locale adibito a cucina, ma, rispetto ad altre tipologie di AFS, la cucina può essere di dimensioni più ridotte in quanto non è necessaria la presenza di container per lo stoccaggio degli alimenti. Infatti, gli ingredienti della razione vengono caricati dall’allevatore in apposite mini-trincee che, grazie a sensori ad ultrasuoni, permettono alla macchina di riconoscere l’alimento e provvederne al caricamento.
Il vantaggio maggiore di questa tecnologia consiste nella possibilità di adibire a cucina un locale di piccole dimensioni, cosa molto utile in allevamenti ove non sia possibile creare un locale idoneo (ad es. siti in zone montuose, oppure caratterizzate da spazi ristretti) oltre ad essere meno costoso.
Conclusioni
L’automazione dell’alimentazione apporta numerosi benefici sotto l’aspetto gestionale (riducendo le necessità giornaliere di manodopera), sotto l’aspetto strutturale (nella progettazione edilizia della stalla) e sotto l’aspetto zootecnico (garantendo un miglioramento del benessere).
Tuttavia, il ricorso a queste tecnologie innovative è oggi ancora limitato principalmente a causa di alcuni ostacoli che nascono dall’integrazione di questi sistemi in realtà strutturali già esistenti; per questo motivo il modello di alimentazione completamente automatizzato di cui si è parlato in questa nota potrebbe costituire una opzione interessante, soprattutto per quegli allevamenti che non dispongono di uno spazio coperto sufficiente da poter destinare allo stoccaggio dei singoli ingredienti della razione.
Inoltre, la completa automazione potrebbe determinare ulteriori vantaggi in termini di manodopera rispetto ad altre tecnologie di Afs dal momento che il carico medio annuo di lavoro per vacca può essere ulteriormente ridotto (> 60%) mentre, rispetto ad un tradizionale utilizzo di un carro miscelatore, il terzo livello di automazione può garantire un risparmio fino al 95% delle ore di lavoro per animale.
A fronte di questa diminuzione del lavoro fisico svolto, l’operatore può dedicare quindi una maggiore attenzione allo svolgimento delle attività di supervisione dell’allevamento, così da poter migliorare la gestione individuale dello stato generale degli animali [Haidn et al., 2017].
In un’ottica di maggiore sostenibilità ambientale e di transizione verso forme di energia rinnovabili, è auspicabile che anche le tecnologie di somministrazione della razione ai bovini si muovano in questa direzione, sfruttando, laddove possibile, l’energia autoprodotta in azienda. Nonostante sia possibile stimare un risparmio del 50% sui costi di esercizio rispetto ad un carro tradizionale con motore a combustione interna, l’attuale diffusione di sistemi Afs o di carri miscelatori tradizionali a trazione elettrica rimane ancora molto contenuta [Repetti, 2018].
Ringraziamenti
Progetto AutoFeed: finanziato dalla Regione Lombardia nell’ambito della sottomisura 16.1 del Feasr – Programma di sviluppo rurale 2014-2020 (www.autofeed.crea.gov.it).
La bibliografia è consultabile contattando gli autori.